Precision CNC Turning Machining Services
Advantages of CNC Turning over Screw Machines
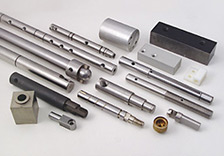
( Click image to enlarge )
CNC lathes use standard turning tools to generate profiles on the outside of a part and boring tools to finish the inside of a part. The machine is programmed to move the cutting tools as needed to generate the desired part shape. These programs are generated either on the machine control or on an off line CAD/CAM system. This combination allows the machine operator to create virtually any shape simply by changing the machine program or a few tools. Since CNC lathes use general purpose tools, set-up time is faster and startup tooling costs are minimal. In addition CNC lathes have the potential to run larger diameter and longer parts than a screw machine. And most importantly CNC lathes are more accurate and maintain better surface finishes. CNC lathes are capable of axis repeatability of within .00015 and are capable of holding part tolerances of .0005.
So why do we need screw machines?
Screw machines are faster. Since CNC lathes use single point tools to “whittle” out the part shape it can sometimes be time consuming. Whereas screw machine can have multiple tools in the cut at the same time. However the increased production must be balanced against the increased set up and tooling costs.
If your part is too large for a screw machine, or if the tolerance are too close, or the lot size is too small then a CNC lathe is the best option. But if it is feasible to run your part on a screw machine, in most cases it will cost less. We do this evaluation on every parts we quote to ensure that we are providing our customer with the best part at the best price.
Our CNC Turning department consists of a variety of two and four axis turning centers complete with hydrostatic bar feeds and sub spindles. We use a DNC program storage system to maintain our part programs. This guarantees consistent part geometry and faster set ups in subsequent production runs. In addition we have several CNC lathes with "gang" style turrets. These machines excel at running small diameter chucker type work with fast cycle times.
Our customer service team will work closely with you to establish an ordering arrangement that is most beneficial to you. We accept blanket orders, as well as supporting Kanban and just-in-time delivery systems.
To learn more about our CNC turning services, please review the table below, or contact us directly.
Past Projects
- Precision CNC Machining of a Stainless Steel Shaft
- High Volume, Tight Tolerance Screw Machining of a Carbon Steel Shaft
- Precision Machined Stainless Steel Bearing Shaft
- Milling, Drilling, & Tapping of a Nylon Roller Adjustment Block
- Precision CNC Turning of a Tool Steel Cleat Cutter
- Screw Machining of a 3030 Stainless Steel Ball Plunger Body
- CNC Turning, Milling, & Light Assembly of an Acetal Piston & Seat Assembly
CNC Turning Machining Capabilities
- Machining Processes
- Turning:
- Contour Turning
Form Turning
Taper Turning - Straight Turning
Facing
Grooving
Threading:- External Single Point Threading
Internal Single Point Threading - Taper Threading
Tapping
Internal Operations:- Drilling
Reaming
Boring
Recessing
Trepanning - Face Grooving
Counter boring
Countersinking
Knurling - Contour Turning
- Capacity
-
- .062" Minimum Diameter
.062" Minimum Length - 6" Maximum Diameter
24" Maximum Length
- .062" Minimum Diameter
- Production Volume
-
- Low Volume
Medium Volume - High Volume
Prototype Leading to Production
- Low Volume
- Tolerance
-
- Straightness: +/- .0003"
Concentricity .0005" TIR - Diameter +/- .0003"
Length + /- .0005"
- Straightness: +/- .0003"
- Finish
- 20 RMS
- Lead Time
- Per Customer Requirement
- Equipment Capabilities
- CNC Control Capabilities
Hydrostatic Bar Feeding
Sub Spindles
- Materials (Metals)
- Alloy Steels (4130, 4140, 4150, 8620, 8650)
Aluminum (2011, 2024, 6061)
Brass
Bronze Alloys
Carbon Steel (1117, 1144, 12L14, 1215, 1018, 1040, 1045)
Copper
Stainless Steel (303, 304, 316, 321, 416, 420, 440C, 17-4)
Tool Steel (A2, M2, D2, S7)
Castings
Forgings
- Materials (Plastic Polymers)
-
- ABS (Acrylonitrile Butadiene Styrene)
Acetyl
Acrylic
Delrin
Fiberglass Reinforced Plastics
Nylon
Phenolic
Polyamide-Imide - Polycarbonate
Polyetheretherketone (PEEK)
Polyetherimide
Polypropylene
Polystyrene
PVC (Polyvinyl Chloride
PTFE
- ABS (Acrylonitrile Butadiene Styrene)
- Inspection
- Per Customer Specifications
Per Ohio Metal Products Standards
- Testing
- Per Customer Specifications
- Documentation
- First Article
Material Certifications
Additional Information
- Industries Served
-
- Appliance
Automotive
Commercial Food Processing Equipment
Electrical
Fixture Components
Government - Industrial Fastening Equipment
Medical
Military
Robotics
Tooling
- Appliance
- Intended Applications
-
- Ball Plungers
Bolts
Collars
Dowel Pins
Fasteners
Guides
Handles
Hubs
Industrial Equipment
Knobs
Machine Components - Punch Blanks
Pulleys
Pins
Screws
Shafts
Sleeves
Spacers
Standoffs
Studs
Vents
- Ball Plungers
- Industry Standards Met
-
- AISI
ANSI
ASME
ASTM - AMS
UNS
SAE
Mil
- AISI